In the realm of manufacturing, a revolutionary technology has emerged, reshaping the way products are designed, developed, and produced. 3D printing, also known as additive manufacturing, has transcended its origins as a rapid prototyping tool to become a disruptive force in industries ranging from aerospace and automotive to healthcare and consumer goods. With its ability to fabricate complex geometries with unprecedented speed and precision, 3D printing is ushering in a new era of innovation and customization.
Understanding 3D Printing
- At its core, 3D printing is a process of building three-dimensional objects layer by layer from digital models. Unlike traditional subtractive manufacturing methods, which involve cutting away material from a solid block, 3D printing adds material sequentially, allowing for greater design flexibility and resource efficiency.
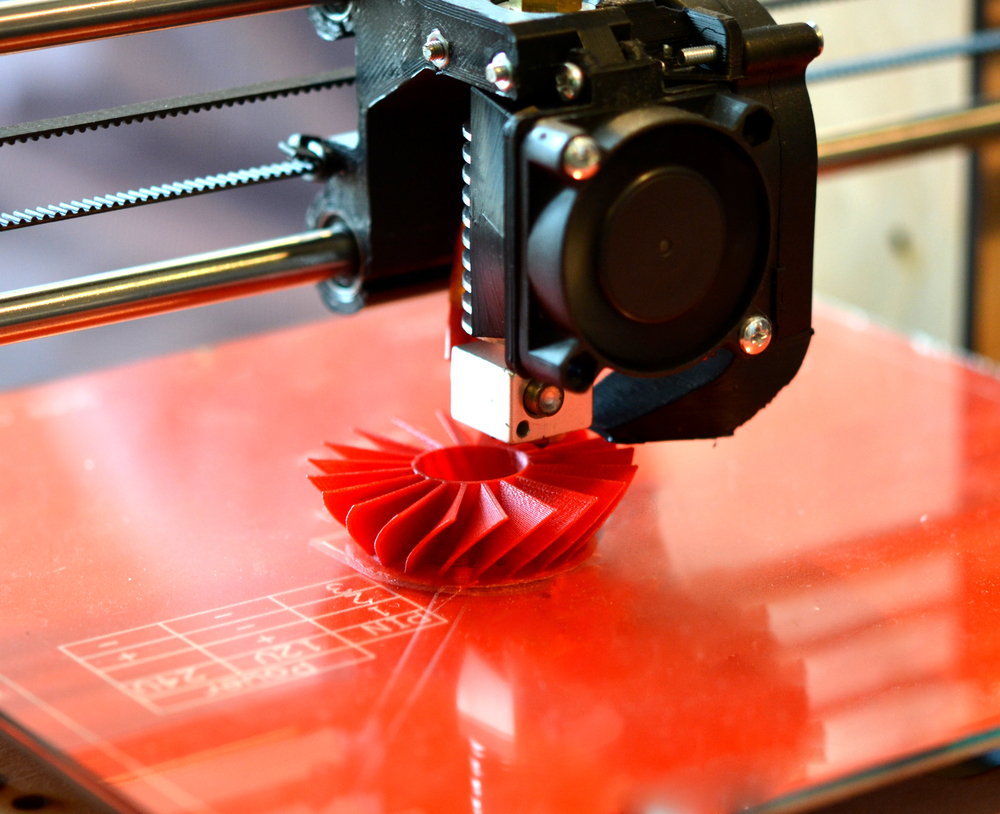
- A digital design is usually produced at the start of the process with computer-aided design (CAD) software. This design is then sliced into thin cross-sectional layers, which serve as instructions for the 3D printer. Using various materials such as plastics, metals, ceramics, and composites, the printer deposits or fuses successive layers of material until the final object is formed.
The Evolution of 3D Printing
- While the roots of 3D printing can be traced back to the 1980s, when the first commercial systems were developed, the technology has undergone significant advancements in recent years. Early 3D printers were primarily used for rapid prototyping purposes, allowing designers and engineers to quickly iterate on their designs and assess functional prototypes without the need for expensive tooling.
- However, as the capabilities of 3D printing technology have matured, its applications have expanded far beyond prototyping. Today, 3D printers are used for everything from custom medical implants and dental prosthetics to architectural models and consumer electronics. Moreover, with the advent of large-scale industrial 3D printers, the technology is increasingly being adopted for end-use production in sectors such as aerospace, automotive, and defense.
Advantages of 3D Printing
The rise of 3D printing can be attributed to several key advantages it offers over traditional manufacturing methods:
1. Design Freedom: Complex geometries that would be difficult or impossible to create using traditional processes can now be created thanks to 3D printing. This design freedom allows for greater innovation and optimization in product development.
2. Customization: One of the most compelling aspects of 3D printing is its ability to produce highly customized and personalized products. From bespoke medical devices tailored to individual patients to custom-fit consumer goods, 3D printing empowers manufacturers to meet the unique needs of their customers.
3. Speed and Efficiency: Traditional manufacturing processes often involve lengthy lead times and significant waste. 3D printing offers rapid turnaround times and eliminates the need for costly tooling, making it a more efficient and sustainable manufacturing solution.
4. On-Demand Production: With 3D printing, products can be manufactured on-demand, reducing the need for large inventories, and minimizing storage costs. This just-in-time manufacturing model enables companies to respond quickly to changes in demand and market trends.
5. Supply Chain Resilience: The decentralized nature of 3D printing allows for distributed manufacturing, reducing reliance on centralized production facilities and mitigating supply chain disruptions. This resilience proved invaluable during the COVID-19 pandemic, as 3D printing was used to produce critical medical supplies such as personal protective equipment (PPE) and ventilator components.
Challenges and Opportunities
- Despite its many advantages, 3D printing still faces challenges that limit its widespread adoption in certain industries. These challenges include limitations in material properties, process speed, and scalability. Additionally, the high cost of industrial-grade 3D printers and materials can be prohibitive for smaller manufacturers.
- However, as research and development efforts continue to drive innovation in the field, the future of 3D printing looks increasingly promising. Advances in materials science, process optimization, and automation are expanding the capabilities of 3D printing and unlocking new applications across industries.
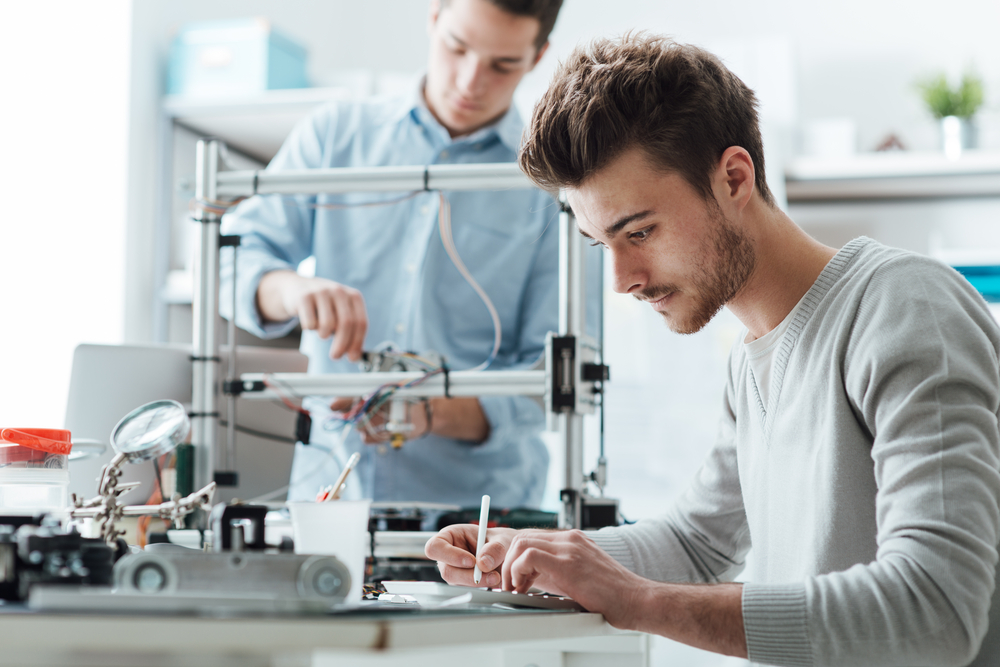
Conclusion
As we stand on the brink of the fourth industrial revolution, 3D printing is poised to play a significant role in shaping the future of manufacturing. From enabling greater customization and sustainability to revolutionizing supply chain organization, the transformative potential of 3D printing is limitless.
As the technology continues to evolve and mature, we can expect to see even greater integration of 3D printing into mainstream manufacturing processes. Whether it is producing complex aerospace components, personalized medical implants, or custom-designed consumer products, 3D printing is paving the way for a more innovative, efficient, and agile manufacturing ecosystem. Welcome to the age of 3D printing, where imagination meets fabrication, and the possibilities are endless.